
1. DESIGN
Our stock includes a range of ring designs, or we can work with you to design a ring that's completely unique.
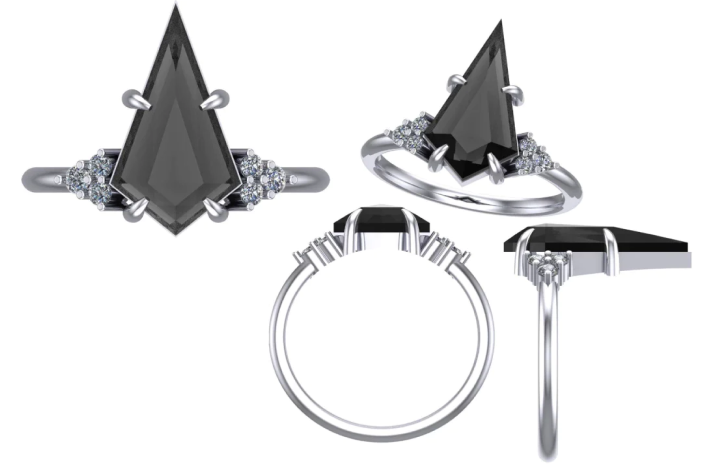
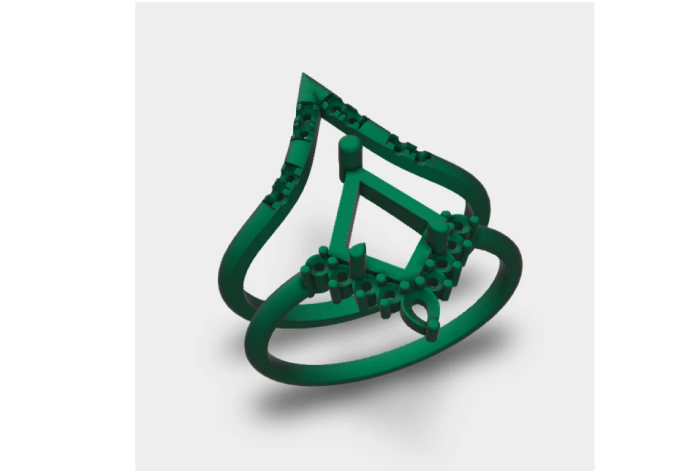

2. CAD
We begin the process of creating a ring by generating a computerized design using CAD software. To ensure precision, we first scan the diamond into the computer and trace its exact measurements, including depth and surface area. As each diamond is unique due to being cut by hand, we cannot reuse the same model twice, and each setting must be custom-made to fit a specific stone. We do not produce settings en masse and insert stones into premade settings, as we believe in crafting each piece with care and attention to detail.

3. MODEL IS MADE
After creating the computerized design of the ring, we utilize 3D printing technology to produce a resin model of the ring. However, we do not rely solely on 3D printing for the production process, as we value the importance of handcrafted work in all of our pieces. In particular, we take pride in the intricate details of each ring, including the placement of tiny diamonds. Rather than casting the diamonds in place, we hand set each one individually and carefully carve the metal seat to ensure a secure and visually appealing setting. For instance, in our Jules and Eliza rings, the "cut down" settings in the band are all done by hand under a microscope, to produce the highest level of precision and quality.
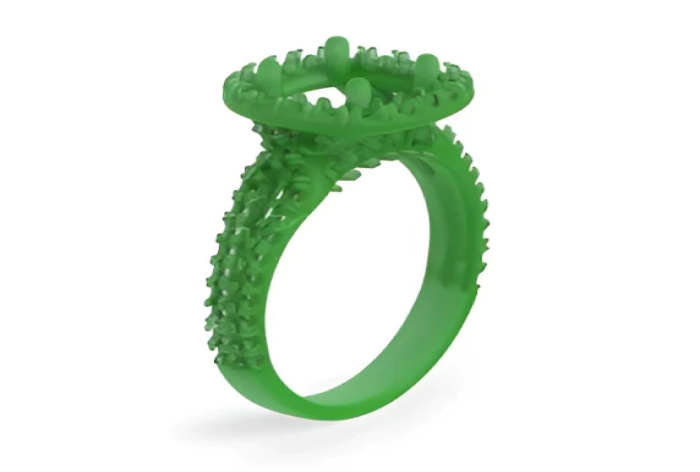
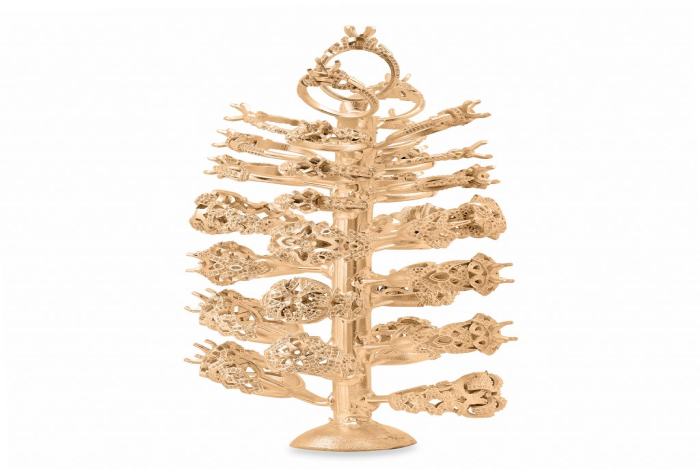

4. TREED UP
The resin ring model is connected to a tiny sprue, which serves as a passage for the molten metal to pass through. Subsequently, it is grouped together with numerous other rings and attached to a larger sprue, forming a tree-like structure.

5. INVESTING
Once the resin model "tree" is prepared, it is placed inside a steel flask. A substance resembling plaster, known as investment, is poured into the flask, covering all the resin models completely.
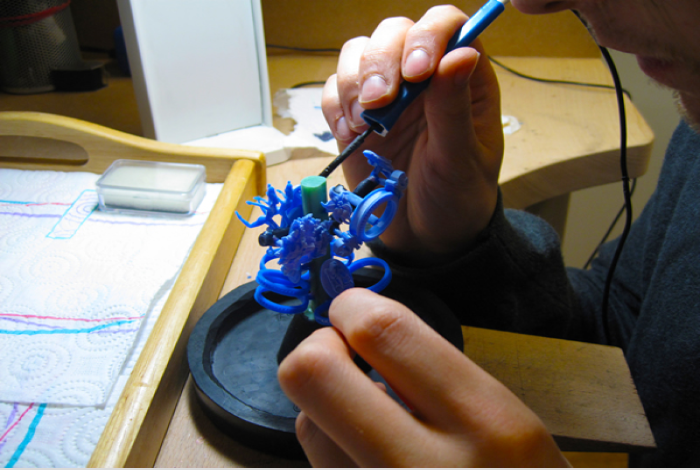
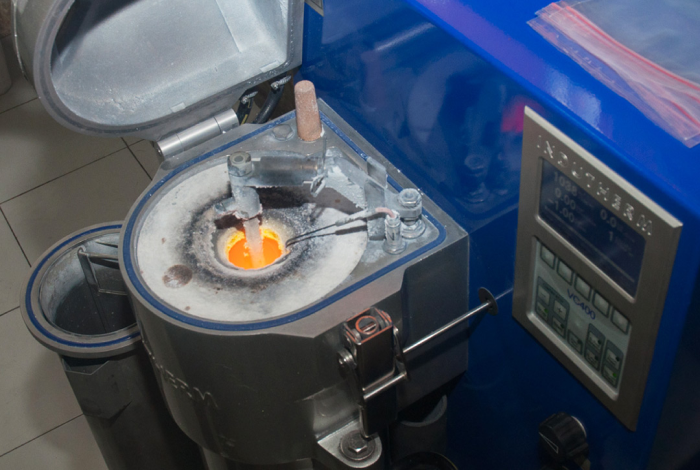

6. BURN OUT
The steel flask containing the resin models is then placed inside a high-temperature oven, where the resin and wax materials are burned out. This step is commonly known as the "lost wax" or "lost resin" process. As a result, cavities are formed within the investment material, corresponding to the shape and size of each ring.

7. GOLD CASTING
The gold is melted down and liquefied either using a machine or a handheld torch. Once in its liquid state, the molten gold is carefully poured into the steel flask. It flows into the cavities that were formed when the resin models were burned out, effectively filling the voids and taking on the shape of the original ring designs.
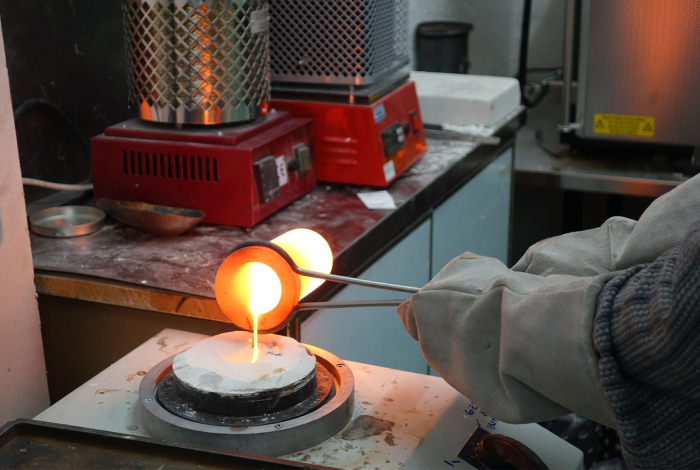
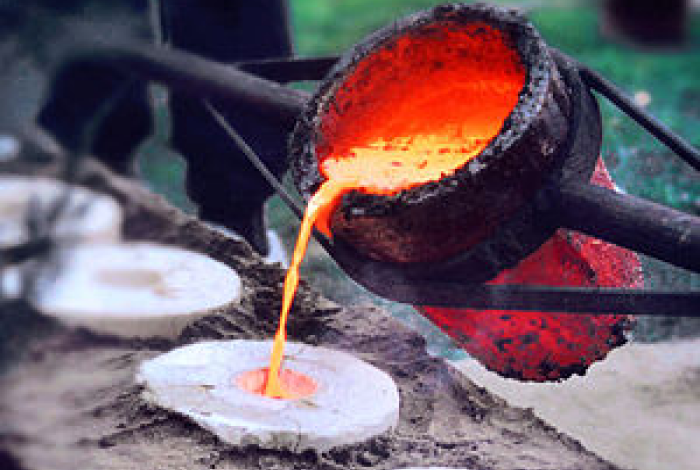

8. COMPLETED FLASK
As the gold is poured into the flask, it fills the cavity and forms a button on top. This button acts as a round cap made of gold, aiding in the uniform cooling of the metal. At this stage, the entire tree of rings becomes a single, solid cast piece, with the gold fully taking the shape of the original designs.

9. QUENCHING
Following the pouring of gold into the hot steel flask, the flask is submerged into a bucket of water. As the flask cools down, steam rises, and the water bubbles, facilitating the removal of the investment material from the metal. Once this process is complete, we carefully retrieve the cast rings from the water. These cast rings are an exact replica of the resin rings that were grouped together on the tree structure.
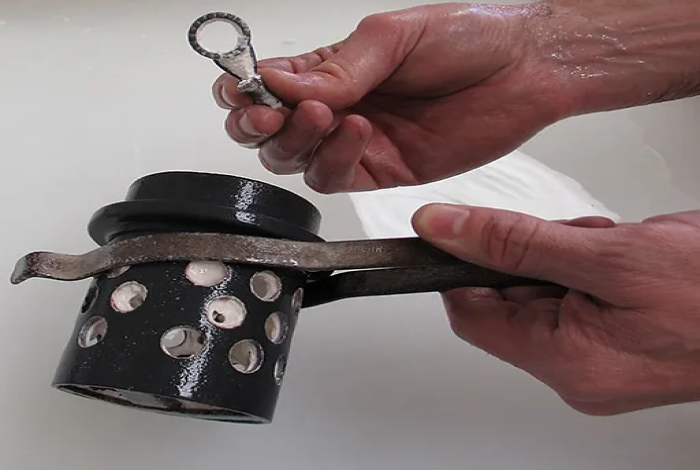
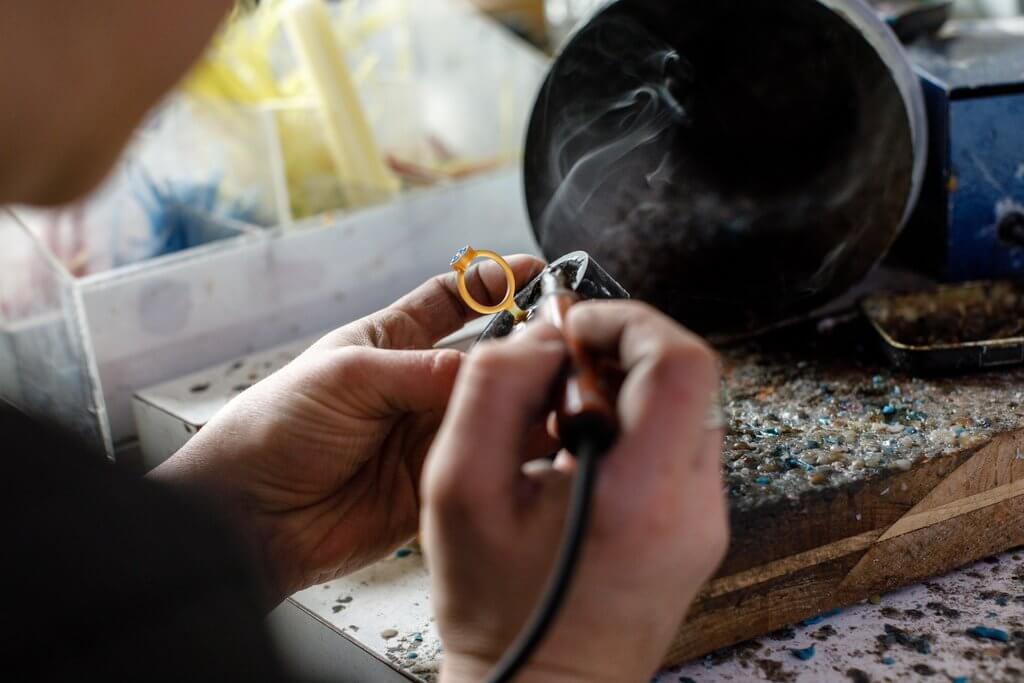

10. CUTTING & CLEANING SUPPORTS
The individual rings are separated from the larger tree by cutting them off. Afterwards, any remaining investment material is thoroughly cleaned off from the surface of the rings.

11. STONE SETTING
Our skilled stone setters utilize various hand-setting techniques, ensuring precision and attention to detail. With the aid of microscopes, each stone is meticulously set. Cut-down setting is used for diamonds in the band, while channel setting, bright setting, and hand-raised bead setting techniques are employed for different designs. The Arwen and Aela setting rings feature delicate Milgrain detailing done by hand, while the Leaf Prong ring showcases intricately hand-engraved leaf vein details. With a combined experience of over 45 years, our stone setters, including our head stone setter trained in the European method, bring exceptional expertise to their craft.
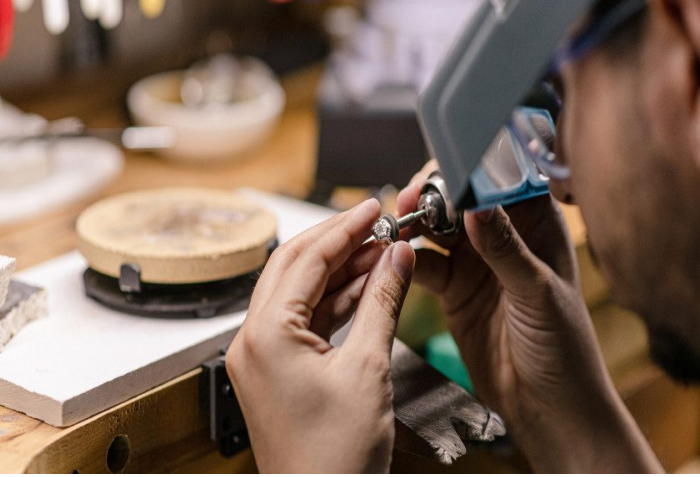